Share this
Free forging has low productivity and a large machining allowance, but the tool is simple and versatile, so it is widely used for forging single-piece and small-batch forgings with simple shapes. Free forging equipment includes air hammers, steam-air hammers, hydraulic presses, etc., which are respectively suitable for the production of a small, medium, and large forgings. Die forging has high productivity, simple operation, and easy mechanization and automation. Die forgings have high dimensional accuracy, a small machining allowance, and more reasonable distribution of fiber structure of forgings, which can further improve the service life of parts.
The basic process of free forging:
During free forging, the shape of the forging is gradually forged from the blank through some basic deformation processes. The basic processes of free forging include upsetting, drawing, punching, bending, and cutting.
1. Upsetting is an operation process in which the raw material is forged in the axial direction to reduce its height and increase its cross-section. This process is commonly used for forging gear blanks and other disc-shaped forgings. Upsetting is divided into two types: full upsetting and partial forging.
2. Lengthening Lengthening is a forging process that increases the length of the blank and reduces the cross-section. It is usually used to produce shaft blanks, such as lathe spindles, connecting rods, and the like.
3. Punching A forging process in which a punch is used to punch through holes or non-through holes in the blank.
4. Bending A forging process in which the billet is bent into a certain angle or shape.
5. Torsion A forging process in which one part of the blank is rotated by a certain angle relative to another part.
6. Cutting The forging process of dividing the blank or cutting off the head.
Die forging The full name of die forging is model forging, which is formed by placing the heated billet in a forging die fixed on the die forging equipment.
The basic process of die forging process: blanking, heating, pre-forging, final forging, punching, trimming, quenching and tempering, and shot peening. Common processes include upsetting, drawing, bending, punching, and forming.
Commonly used die forging equipment includes a dying forging hammer, hot die forging press, flat forging machine, and friction press.
In layman’s terms, the quality of forged flanges is better, generally produced by die forging, with fine crystal structure and high strength, of course, the price is also more expensive.
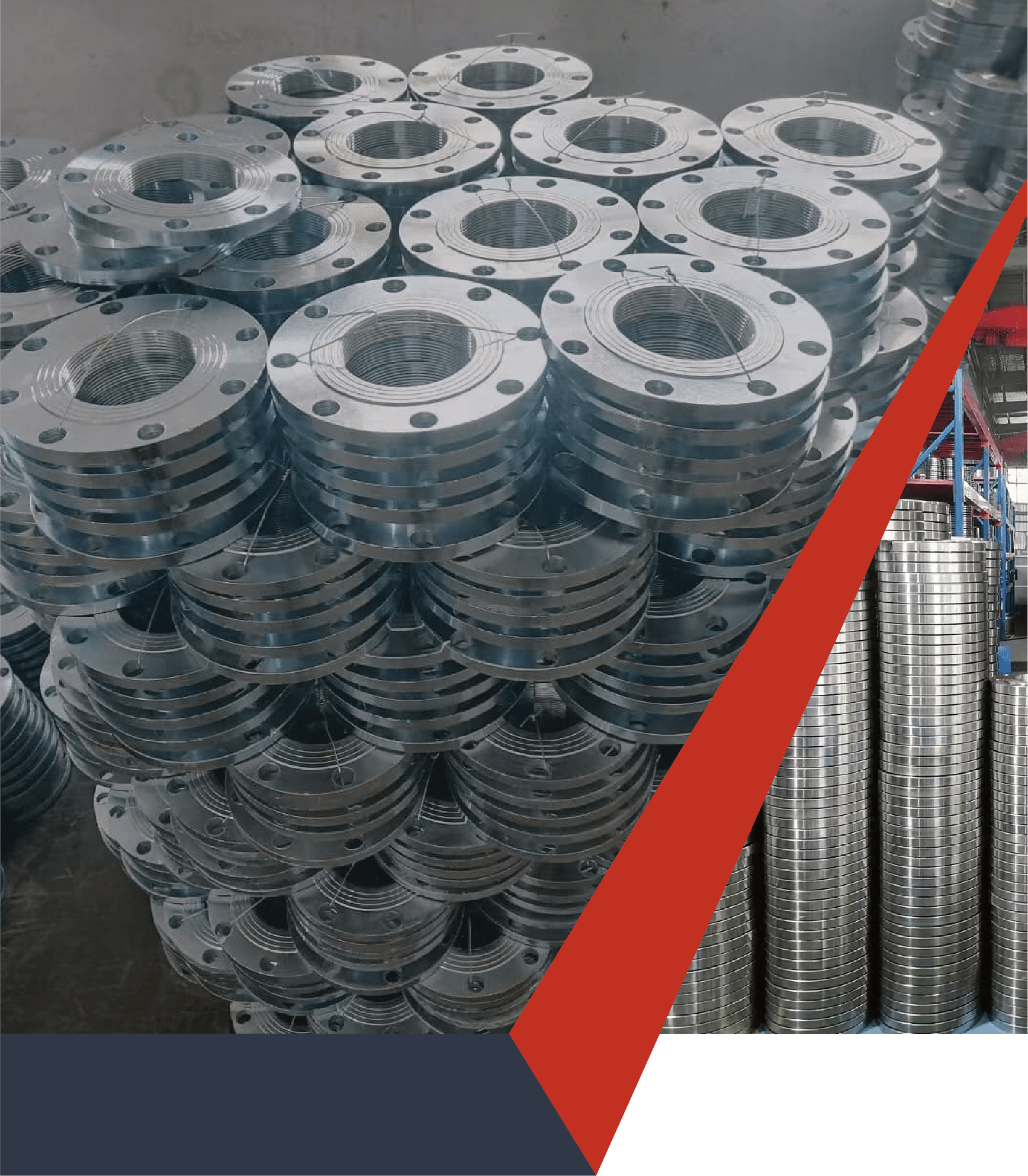
For pipe fittings, please link: https://bekingpiping.com